MES w epoce Przemysłu 4.0
-
- 07.05.2018, godz. 11:10
Aplikacje wspomagające realizację produkcji są integrowane z kolejnymi rozwiązaniami i coraz częściej użytkowane w chmurze. Nowe funkcje systemów MES pozwalają na bezproblemowe uruchamianie krótkoseryjnej produkcji i ograniczenie awarii dzięki predykcyjnej analizie danych.

Coraz większe potrzeby firm produkcyjnych w zakresie monitorowania procesu produkcji i zbierania danych w czasie rzeczywistym powodują stałe zapotrzebowanie na systemy realizacji produkcji (MES, Manufacturing Execution Systems). Jak wynika z raportu MarketsandMarkets „Manufacturing Execution System Market by Deployment Type (On-Premises, On-Demand and Hybrid), Offering (Software and Services), Process Industry (Food & Beverages, Oil & Gas), Discrete Industry (Automotive, Medical Devices) – Global Forecast to 2022”, w 2020 r. wartość rynku MES wyniesie 12,6 mld USD, jego średnioroczny wzrost do 2022 r. będzie się utrzymywał na poziomie 10,8%, a w sektorze przetwórstwa żywności CAGR będzie jeszcze wyższy: 14,3%. Największy wzrost rynku rozwiązań MES jest oczekiwany w Ameryce Północnej w związku z zapotrzebowaniem na systemy realizacji produkcji z takich branż, jak: oczyszczanie wody i ścieków, żywność i napoje, energetyka.
Popyt na oprogramowanie będzie rósł także w Europie, w tym w Polsce, gdzie obecnie w pełni zautomatyzowanych jest jedynie 15% fabryk, a wiele zakładów produkcyjnych wciąż nie ma profesjonalnych narzędzi do zarządzania produkcją.
Zobacz również:
W 2016 r. firma BPSC przeprowadziła badanie wśród 180 decydentów z dużych i średnich firm w naszym kraju, pytając ich o rozwiązania do planowania i monitorowania produkcji. Jedynie 67% respondentów posiadało system ERP (z których połowa miała ograniczone funkcjonalności), a 47% nadal planowało produkcję w arkuszach kalkulacyjnych. Zakładając, że w ciągu niecałych dwóch lat odsetek ten się zmniejszył, to i tak nie jest dobrze. Pole do wdrożeń MES jest więc bardzo duże.
Za wdrożeniami MES przemawiają osiągane korzyści. Analitycy firmy badawczej Gartner podkreślają zwłaszcza poprawę jakości o 84%, redukcję cykli produkcyjnych o 82%, zmniejszenie kosztów pracy o72% – a wszystko to jest do osiągnięcia w skali jednego roku. Duże oszczędności zyskuje się już na samej redukcji nieplanowanych przestojów oraz zwiększeniu wydajności dzięki skróceniu cyklu wytwórczego.
Systemy ERP i MES zasilane są ogromną ich ilością danych pochodzących z różnych źródeł – wewnętrznych i zewnętrznych. Badanie Panorama Consulting pokazało, że aż 72% respondentów jako główny powód, dla którego nie decyduje się na chmurę, podało ryzyko utraty dostępu do danych. Rozwiązaniem problemu jest system hybrydowy.
Paweł Sokólski z Wydziału Elektrotechniki i Automatyki Politechniki Gdańskiej w pracy z 2017 r. „Zaawansowane systemy informatyczne w zakładach przemysłowych” podaje przykład zwiększenia efektywności pracy dzięki skróceniu cyklu produkcyjnego. Jeżeli cykl obliczany przez maszynę (producenta) wynosi 4,5 sekundy, w ciągu jednej zmiany produkuje się 6400 sztuk wyrobów, a co 40 sztuk następuje 14 sekund przestoju, to po przeprogramowaniu maszyny dzięki systemowi MES cykl produkcyjny można skrócić do 4,18 sekundy. Daje to dodatkowe 495 sztuk dziennie. Zakładając zysk na poziomie 0,20 zł przy 3 maszynach pracujących na 2 zmiany, po 100 dniach pracy zwraca się system za ok. 60 000 zł.
Wybór rozwiązań Manufacturing Execution Systems jest obecnie bardzo duży. Raport Global Industry Analysts wymienia 64 firmy znaczące na tym rynku, a Capterra, globalny serwis biznesowy, który pomaga firmom znaleźć właściwe oprogramowanie, opisuje ok. 100 takich systemów. Lista głównych graczy jest jednak dość krótka. Na rynku dominują: ABB (Szwajcaria), Andea Solutions (Polska), Dassault Systemes (Francja), Emerson Electric (USA), General Electric Company (USA), Honeywell International (USA), Rockwell Automation (USA), SAP AG (Niemcy), Schneider Electric (Francja), Siemens AG (Niemcy), Werum IT Solutions GmbH (Niemcy) i Yokogawa Electric (Japonia).
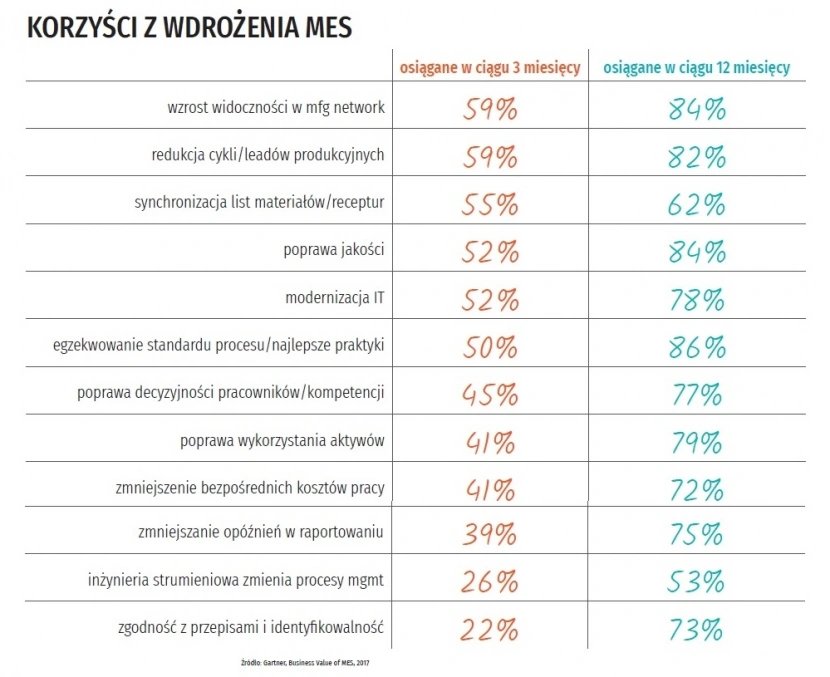
W stronę Przemysłu 4.0
Podobnie jak większość systemów informatycznych, również MES podlega dziś istotnym zmianom. Bez wątpienia trendem, który determinuje jego rozwój, jest idea Przemysłu 4.0. To zbiorcze pojęcie oznacza integrację inteligentnych maszyn i systemów oraz wprowadzanie zmian w procesach produkcyjnych mające na celu zwiększanie wydajności wytwarzania, elastyczność produkcji oraz opłacalność produkcji krótkoseryjnej. W tym celu MES wykorzystuje najnowsze technologie, m.in. internet rzeczy (IoT). Do 2021 r. przychody na rynku przemysłowego IoT będą rosły średnio o 27% rocznie, osiągając wartość ponad 20 mld USD – trzy razy więcej niż obecnie. Celem wdrażania rozwiązań IoT w przemyśle jest dostarczenie przedsiębiorstwu cyfrowej pętli zwrotnej (digital closed-loop), dającej informacje o procesach, operacjach i produktach.
Kolejnym trendem jest implementacja technologii Machine Learning. Uczenie maszynowe poprzez analizę danych obecnych i historycznych pozwala systemowi MES przewidzieć, kiedy mogą wystąpić problemy na linii produkcyjnej lub awarie sprzętu. „Zaawansowana analityka danych umożliwia Preventive Maintenace. Systemy chmurowe (np. Microsoft Azure) mają wbudowany moduł Machine Learning, więc w łatwy sposób można go zastosować w swoich rozwiązaniach. Istotne jest również to, że producenci maszyn idą w stronę łatwiejszego udostępniania informacji o statusie urządzeń, co pozwala na uzyskanie jeszcze większej ilości danych. W sterowniku maszyny zawarte są wszystkie jej parametry. Wystarczy przy wymaganiach dotyczących parametrów maszyny dodać opcje ich eksportu do systemów zewnętrznych, np. do MES” – mówi Paweł Kaleta, inżynier systemów automatyki w DSR SA.
Postępuje też automatyzacja systemów MES i głębsza integracja z różnego typu rozwiązaniami do planowania produkcji, narzędziami projektowymi oraz ERP. „MES coraz częściej integrowany jest z automatyką czy narzędziami klasy PLM do zarządzania życiem produktów, a także narzędziami authoringowymi 3D, takimi jak: Visual Enterprise, CAD czy Autodesk. Dzięki ich wykorzystaniu możliwe jest monitorowanie pracy urządzeń i zbieranie w czasie rzeczywistym informacji, które wpływają na wyniki produkcji. Systemy MES w najbliższych latach będą się charakteryzować większą automatyzacją, i to one będą sterować całą produkcją” – twierdzi Tomasz Kołodziejak, Business Solution Architect, SAP Polska.
Przykładem wdrożenia, w którym MES współpracuje z innymi systemami, jest rozwiązanie w firmie BRP-Rotax, oferującej silniki do skuterów śnieżnych. Cały proces produkcji i poszczególne urządzenia są tam zintegrowane z danymi zawartymi w systemie SAP ERP. Informacje o kolejnych etapach tworzenia produktu są wizualizowane w czasie rzeczywistym na interaktywnych wykresach. Wszystko to pozwala usprawniać szybkość i precyzję produkcji MTO (Make To Order – produkcja na zlecenie), czyli wytwarzania różnych silników z różną konfiguracją na tej samej linii produkcyjnej.
MES przenosi się w chmurę
Jeśli chodzi o model wdrożeń systemów MES, to coraz częściej jest to cloud computing. Jak przewiduje IDC, do 2020 r. 60% firm produkcyjnych na świecie będzie opierać swoją pracę na cyfrowych platformach w chmurze.
Organizacja rozważająca przeniesienie MES do chmury na pewno dostrzeże korzyści finansowe związane m.in. z elastycznym skalowaniem produkcji, zamiast skalowania jedynie do poziomu maksymalnego obciążenia. Przechodzenie w chmurę związane jest również z takimi aspektami, jak:
• Globalne i złożone łańcuchy dostaw wymagające nowych strategii IT.
• Analityka w czasie rzeczywistym: decyzje biznesowe muszą być podejmowane szybko dzięki analizie dużych zbiorów danych, które są szybko dostępne dla użytkownika urządzenia.
• Technologia Mission Critical z zaawansowanym przywracaniem systemu po awarii: zwiększona zależność Mission Critical od technologii w produkcji zwiększyła potrzebę dodatkowych możliwości przetwarzania i odzyskiwania po awarii.
• Zmiany rynkowe wymagające maksymalnej sprawności: elastyczność produkcyjna, która sprawia, że wielkość partii, choćby wynosiła kilka sztuk, musi być możliwa do wytworzenia.
• „Best of Breed”: aplikacje monolityczne okazały się niewystarczające, a poszczególni producenci mają najlepsze w swojej klasie technologie, często łatwo dostępne w opcji chmury.
Przykładem firmy czerpiącej korzyści z chmury MES jest Autoliv, dostawca systemów bezpieczeństwa samochodowego. Obecnie korzysta z tej technologii w 82 obiektach w 27 krajach. Wdrożenie MES w chmurze spowodowało w Autoliv 30-proc. wzrost czasu reakcji na problemy związane z konserwacją, 5-proc. poprawę dostępności operacyjnej i 12-proc. spadek kosztów części zamiennych.
MES w chmurze jest narzędziem nie tylko dla dużych firm, ale także dla średnich i małych producentów, którzy nie posiadają rozbudowanej infrastruktury ani zasobów IT. Dzięki chmurze mają szansę na korzystanie z zaawansowanych, wcześniej niedostępnych rozwiązań
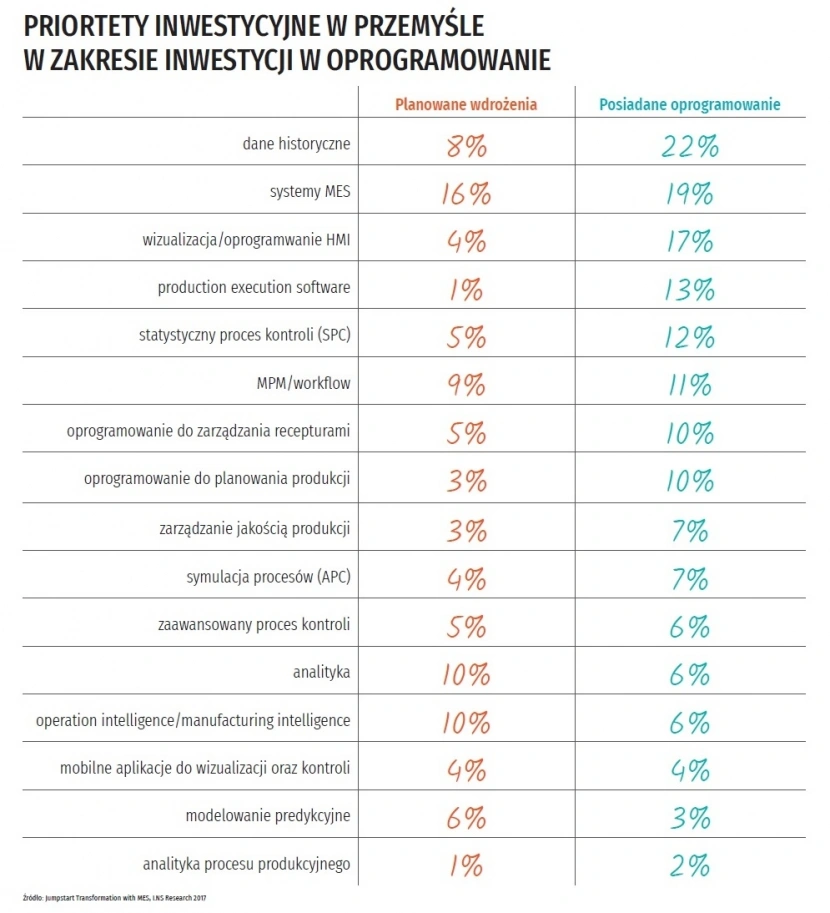
Co hamuje przejście w chmurę?
Chmura budzi jednak obawy użytkowników. Są to zarówno blokady mentalne wynikające z braku informacji (np. na temat bezpieczeństwa), jak i rzeczywiste problemy związane z dostępnością. Liczba wdrożeń cloud MES zależy m.in. od tempa rozwoju infrastruktury technicznej, ponieważ zaawansowane rozwiązania cloud computing potrzebują stabilnego i szerokopasmowego dostępu do internetu, a z tym bywa różnie. „W dużych aglomeracjach infrastruktura nie wygląda źle, ale w mniejszych ośrodkach pozostawia wiele do życzenia. Bez działań systemowych związanych z poprawą infrastruktury dostępowej niewiele da się jednak osiągnąć. Wiele zakładów produkcyjnych budowanych jest w miejscach, w których nie ma dostępu do dobrej jakości łączy, a co za tym idzie, nawet jeśli firmy myślą o implementacji rozwiązań chmurowych, to nie mogą ryzykować braku dostępu do swoich danych przetwarzanych w chmurze” – mówi Przemysław Kędzierski, Product Owner obszaru Produkcja w BPSC.
Coraz częściej modelem wdrożeń systemów MES jest cloud computing. Jak przewiduje IDC, do 2020 roku 60% firm produkcyjnych na świecie będzie opierać swoją pracę na cyfrowych platformach w chmurze.
Inną kwestią jest bezpieczeństwo informacji. Systemy ERP i MES zasilane są ogromną ich ilością danych pochodzących z różnych źródeł – wewnętrznych i zewnętrznych. Badanie Panorama Consulting sprzed kilku miesięcy pokazało, że aż 72% respondentów jako główny powód, dla którego nie decyduje się na chmurę, podało ryzyko utraty dostępu do danych. Te obawy nie do końca są poparte faktami, a zachowawcze podejście do cloud computingu często wynika z braku wiedzy i doświadczenia w korzystaniu z tego typu technologii.
Rozwiązaniem problemu z bezpieczeństwem jest system hybrydowy. Model ten umożliwia przepływ pracy pomiędzy chmurami prywatnymi i publicznymi, a także pomiędzy chmurą a rozwiązaniami on-premise. „W systemie hybrydowym aktualne dane i parametry są przechowywane zarówno na serwerze w firmie, jak i w chmurze, natomiast wszystkie dane historyczne przetrzymywane są tylko na chmurze. Dzięki temu nie potrzebujemy wielkich serwerów do przetrzymywania danych, a w razie problemów z połączeniem aktualne dane i parametry mamy na serwerach wewnętrznych. Dodatkowo serwer wewnętrzny może filtrować dane i przesyłać do chmury tylko te, które warto zarchiwizować. Służy wtedy jako gateway dla przetwarzanych danych” – mówi Paweł Kaleta z DSR.
ERP czy MES?
Pytanie o to, co wybrać: moduł ERP czy samodzielny system MES, nie należy może do pytań o być albo nie być, ale wciąż powraca. Jak twierdzą eksperci, trudno jednoznacznie stwierdzić, czy lepiej zdecydować się na system klasy ERP czy samodzielne rozwiązanie MES. Jedno jest pewne: systemy ERP nie są zaprojektowane z myślą o hali produkcyjnej, nie są aplikacjami czasu rzeczywistego. Brakuje im szybkości reakcji in real time. Są systemami bardziej statycznymi i mają znaczące opóźnienie. Natomiast systemy MES są szybkie i pozwalają na podejmowanie decyzji w czasie rzeczywistym. Oba systemy realizują inne cele, a maksymalizacja efektów ich wykorzystania bazuje na ich współpracy. W przedsiębiorstwie, które posiada system ERP i planuje wdrożyć MES, zarówno moduł produkcyjny systemu ERP, jak i oprogramowanie MES znajdą zastosowanie, ale należy mieć świadomość, jakie są między nimi różnice i do jakich celów zostały one stworzone.
Systemy ERP nie są zaprojektowane z myślą o hali produkcyjnej, nie są aplikacjami czasu rzeczywistego. Są systemami bardziej statycznymi i mają znaczące opóźnienie. Systemy MES są szybkie i pozwalają na podejmowanie decyzji w czasie rzeczywistym. Oba systemy realizują inne cele, a maksymalizacja efektów ich wykorzystania bazuje na ich współpracy.
Dobrą informacją dla klientów jest to, że systemy MES przestawiły się z monolitycznych systemów na rozwiązania modułowe, co oznacza, że organizacje mogą wybrać, które funkcje są dla nich najważniejsze i zapłacić tylko za nie.